Energy efficiency in manufacturing (non-durable)
Energy costs are a big part of fixed costs in this sector so any measure taken to be more efficient can help with budget certainty. You might be doing some of the no cost steps already, but we have a few suggestions for low-cost and investment-based options which could make a real difference to your energy management.
Showing commitment to the environment could also boost staff morale and help you retain them for longer. Being proactive about energy efficiency measures and taking steps to reduce your consumption could result in bills that are 18-25% lower, getting your investment back in less than 18 months.
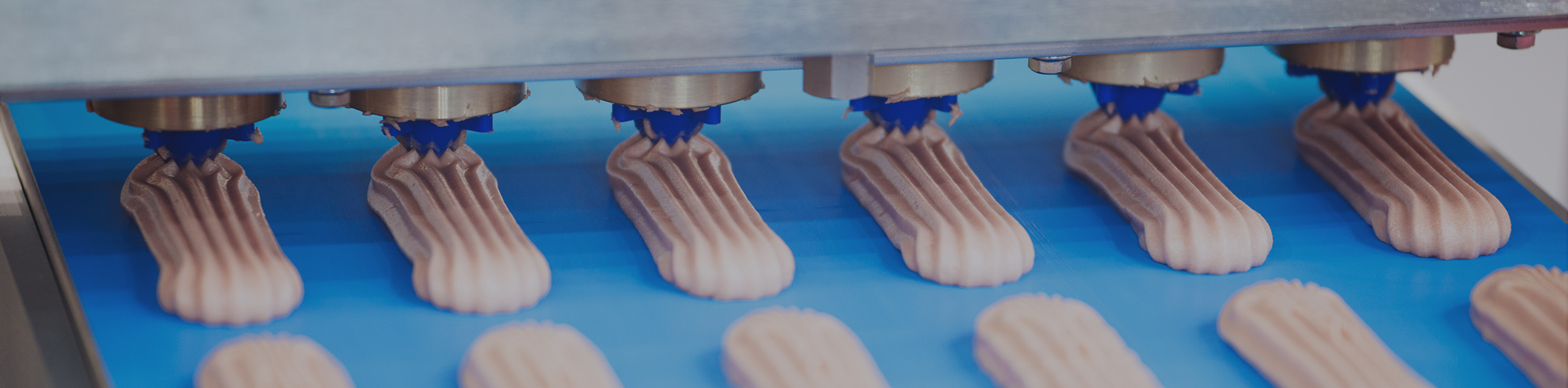
Who is this for?
Food processing businesses
Drink processing businesses
Other consumables or short-life product producers
Simple no cost changes
Straightforward low-cost changes
Long-term savings from the right investments
For larger savings from energy efficiency you might need to spend some money upfront, especially when you’re planning refurbishments already.
Action plan
Start by making a note of your current consumption.
By default, your smart meter will record consumption data in 30-minute intervals. You can use this starting point as a benchmark.
Do you notice any variations during the year?
Make a note of them and think about what could cause them. For example, if your business is affected by the weather, you could save energy by investing in better insulation and save money in the long term.
Benchmark your current energy use
How does it compare to last year or last season? Make sure you analyse similar time periods (for example, December 2018 with December 2019) to make sure the improvement in efficiency isn’t influenced by other factors.
How much are you going to reduce your consumption by?
Set a realistic goal and a target date of when you’ll measure consumption again to track how you’re doing.
Choose the steps you’ll take to achieve those goals
Use the categories above to put advice into practice and involve your employees. To motivate staff, try to make it into a competition. Why not offer a free meal out to the team that comes up with the most energy saving ideas or commit to donating the savings to a local charity that they choose?
Make the changes and measure the results
Communicate all improvements with your staff, no matter how small, to encourage an energy efficient state of mind. And when you're ready to make more changes to become energy efficient, come back to this action plan and start again.
The facts, figures and advice have been sourced from the Carbon Trust, Energy Trust and the Department for Business, Energy and Industrial Strategy (formerly known as the Department of Energy and Climate Change).